Research and Development
Itinerant Machinery
Itinerant machinery allows for the optimization and improvement of the valorization at the EVUP Network.
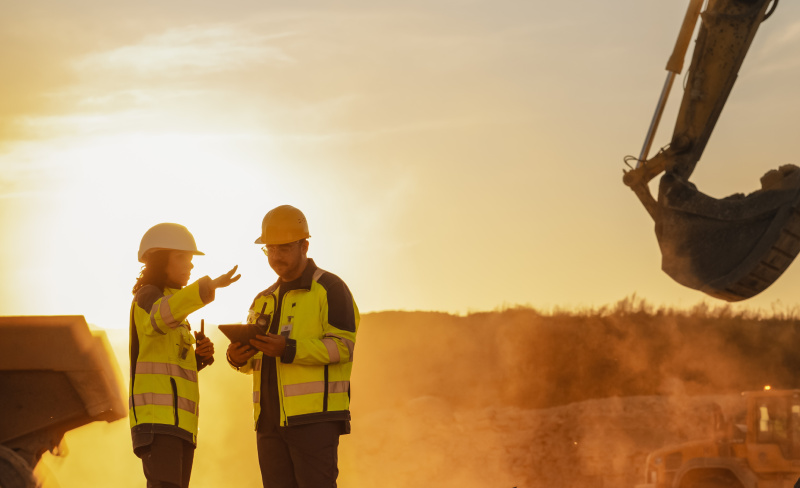
What is Itinerant Machinery?
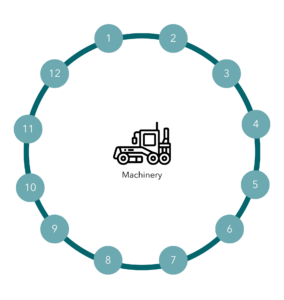
What are the Movements of Itinerancy?
The itinerancy process can vary based on the collected RPJ (Residues from Pruning and Gardening) in different communities and can also be influenced by climate conditions. The itinerant machines responsible for maintaining the material during the valorization process are specialized for different stages. Resting periods at a station can last up to a month and a half, and multiple batches of material may be at different stages of the process simultaneously, requiring careful coordination.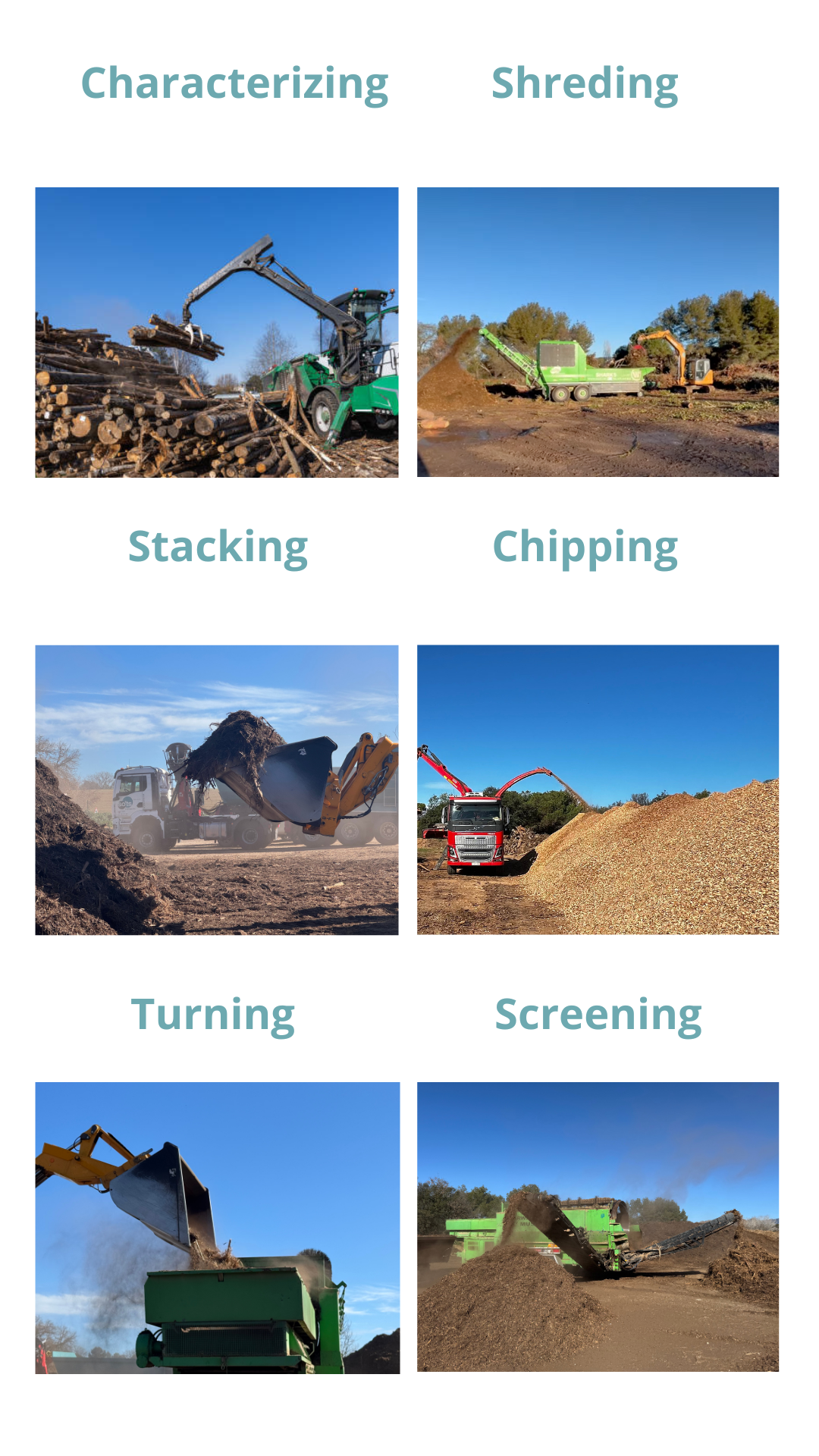
The Environmental and Economic Impact of the Itinerant Machinery System
Objective: Evaluate the environmental and economic impact of using itinerant machinery compared to a fixed machinery system.
Methodology:
- Conduct a life cycle analysis (LCA) to compare carbon emissions and other environmental impacts of both systems.
- Collect data on operating, maintenance, and transport costs associated with itinerant and fixed machinery.
- Conduct interviews with operators and managers of Self-Managed EVUPs to gather qualitative feedback on the effectiveness and challenges of each system.
- Develop recommendations for the continuous improvement of the itinerant machinery system based on the results obtained.
Expected Impact: Identification of best practices to minimize environmental impact and maximize the economic efficiency of the EVUP Network, contributing to a more sustainable management of plant waste.
Optimization of Itinerant Machinery in the Valorization of Pruning and Gardening Waste (RPJ)
Objective: Analyze and optimize the movements and use of itinerant machinery across the different stations of the EVUP Network to maximize the efficiency of the plant waste valorization process.
Methodology:
- Collect data on the resting and processing periods of each type of waste at various stations.
- Develop logistical models to optimize machinery movements.
- Implement the proposed solutions and evaluate their effectiveness through field tests.
- Compare costs and operational efficiency before and after the implementation of improvements.
Expected Impact: Improved coordination and use of machinery, reduced operational and transport costs, and increased efficiency in the valorization of plant waste.